Zusammenfassung
About the Role
Logistic Coordination
- Fully support project relevant goods delivery to RLT Haiyan Site on time with well accommodation including goods importation, transportation, relevant customs authority affairs.
- Work with platform SCM to coordinate door to door product material delivery to RLT Haiyan site.
- Site SPOC to ensure smooth finished product delivery within China.
S&OP management
- Introduce monthly S&OP process in accordance with the NOSSCE policy on the S&OP process
- Contributes to the demand Review with the customer (Global Supply Chain Management) in order to identify major changes and trends (ie products, volumes) to be taken into account in the site's “Supply Review”
- Facilitate the cycle and the monthly meeting of “Demand Review” (DR) and assesses and if necessary challenges the figures relating to the request, and ensures that the changes in demand (the quantities to be supplied, the dates of need and the priorities in particular) are clear and well communicated at the site level
- Reviews the macro plan of the manufacturing capacities of the site (“Rough Cut Capacity Plan”, RCCP) and the resource planning for the tactical horizon (from 4 to 24 months minimum), according to the families of established products
- Facilitates the search for alignment at site level in the case of divergent proposals concerning the use of the site's capacities in the medium and long term, by identifying in particular slots available in production and by facilitating the sharing of resources (staff, equipment, material) with the support of the Manufacturing unit Heads
- Facilitates for the Site Supply Chain Manager the monthly Supply Review (SR) meeting and ensure a manufacturing plan is proposed, aligned with the different actors and taking into account the constraints, risks and additional resource needs if necessary
- Participates in the preparation and the holding of the Integrated Reconciliation meeting with BPA (“Integrated reconciliation”, IR) and supports the financial viability of the proposed plan, including the calculation of personnel needs (FTEs)
- Proposes the optimal supply plan to SLT for approval during the Management Review, in accordance with the site objectives; this plan will be based on clearly formulated manufacturing hypotheses with accurate and up-to-date information from all the sectors concerned, including alternatives, risks and opportunities
- Responsible to translate the demonstrated Site process capability into accurate planning parameters (e.g. yield and BOM adjustment, TPT & TPLT review)
- Act as point of escalation for SC issues assuring operational scheduling is executed according the priorities as part of bottleneck management
Warehouse Management and Inventory Management
- Management on onsite warehouse and Finished Products shipment plan.
- Product related material ordering and material inventory management.
- Support the routine activities for onsite GSP warehouse after future establishment.
Change and Transformation Leadership
- Develop and implement strategy aligned with NTO strategy
- Ensure optimal collaboration and synergies among various units to continuously improve internal processes and seamlessly fulfill business objectives
- Lead site industrial transformation journey and build-up site road map to ensure durable competitiveness
- Role model the culture aspiration of being Curious, Inspired, Unbossed, Self-Aware
- Be a learner, not a knower
- Be clear, present and focused
- Develop trusting and respectful relationships
- Manage your energy and impact
- Engages and motivates the units and delivers strong results with an empowered team
- Support the Manufacturing Head to develop, review and enhance Operational schedulers planning capabilities
Operational excellence and continuous improvement
- Develops and follows-up the medium and long term Site strategy in accordance with the strategic vision of the site and Novartis Technical Operations
- Coordinate/Lead the strategic projects from site (incl. transformation relevant)
- Responsible for project management methodology implementation, project governance and resource management
- Responsible for Site KPI consolidation
- Drives OpEx opportunities identification and OpEx project portfolio
- Sponsor OpEx initiatives
- Promote an OpEx culture and best practice sharing
- Builds/sustains strong network in and outside the organization and with the operations center
Coordination (internal and external)
- Coordinate activities between Global Operations Centers (GOCs) and the site. Ensure right level of collaboration in place
- Coordinate site requirements to determine /adjust the level of service or new request required from (GOCs)
- Responsible for consolidation and reporting of site KPIs
- Lead BC (Business Continuity) agenda of the site in interaction with (GOCs)
- Ensure NOSSCE standards sustainability at Site regarding Shop Floor Control process
Digital Curiosity
- Explore the potential of data and technology to support transformation journey of the manufacturing site in-line with NTO strategy
- Encourage others to learn about and leverage data and technology
HSE & Quality
- Ensure all activities in compliance with cGxP, incl. data integrity
- Comply with all HSE guidelines
- Detect and report potential accident, risks and propose solutions
- Responsible for participating in initial training and retraining
Why Novartis: Helping people with disease and their families takes more than innovative science. It takes a community of smart, passionate people like you. Collaborating, supporting and inspiring each other. Combining to achieve breakthroughs that change patients’ lives. Ready to create a brighter future together? https://www.novartis.com/about/strategy/people-and-culture
Join our Novartis Network: Not the right Novartis role for you? Sign up to our talent community to stay connected and learn about suitable career opportunities as soon as they come up: https://talentnetwork.novartis.com/network
Benefits and Rewards: Read our handbook to learn about all the ways we’ll help you thrive personally and professionally: https://www.novartis.com/careers/benefits-rewards
Accessibility and accommodation
Novartis is committed to working with and providing reasonable accommodation to individuals with disabilities. If, because of a medical condition or disability, you need a reasonable accommodation for any part of the recruitment process, or in order to perform the essential functions of a position, please send an e-mail to [email protected] and let us know the nature of your request and your contact information. Please include the job requisition number in your message.
Novartis is committed to building an outstanding, inclusive work environment and diverse teams' representative of the patients and communities we serve.
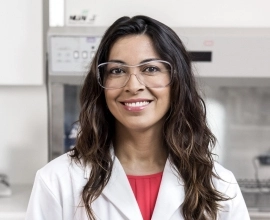